Cycle Counting: Inventory Audit in SAP Business One
Introduction
Cycle Counting is a necessary action in inventory management. The implication of wrong inventory can be grave for a company. It not only mislead in the available stock quantity, but also in the actual stock value - accounting. A number of practices can be leveraged when auditing inventory, however, in this paper, I intend to explore cycle counting as an inventory audit tool. This subject topic will be discussed in the following parts: The Concept, Why Inventory Audit, Frequency of Audit, When to Audit, The Process in SAP Business One and Recommendations.
The Concept
A few months ago, my colleague and I went for a management demo of SAP Business One for a leading bookshop in Nigeria. And you know what? The Chief Financial Officer asked a fundamental question: What happens if I've got some stocks physically in my warehouse and the system displays zero stock, will I be able to sell? What's on your mind, negative stock management? Well, that concept is a topic for another posting. Well, for me, what struck me was inventory record inaccuracy. The nightmare of an entrepreneur among other things includes the correctness of his stock record, hence the need for a stock auditing infrastructure like Cycle Counting. This kind of system is provided in SAP Business One.
Thus, it is expedient that inventory be counted at defined intervals and if variances occur, it should be reconciled. The process of inventory audit follows some sequential steps as detailed below.
1. Print out the inventory status from the system
2. Perform the physical count of the item and record your findings
3. Ascertain the correctness of the count by recounting
4. Record the count result in the system
5. If variances occur, post the stock difference.
As a matter of fact, inventory records are not always 100% accurate. Variances do occur, depending on the item type, volatility and frequency of movement. Hence, tolerance (in %) can be defined to cover this lapse. However, as much as possible, 100% accuracy should be the target.Why Inventory Audit The need for inventory audit is enormous. Broadly, inventory audit is of great interest and importance to two sets of people in a firm - the Financial Controller and the Planning Manager. While the Financial Controller is concerned about the accuracy of the stock value, the Planning Manager is concerned about the accuracy of the stock quantity. In whichever way you look at it, the stock quantity is the driver of the stock value. For the Financial Controller to know the correct stock value, the stock quantity must have been duly counted and multiplied by the cost of the item.
From the foregoing therefore, we can safely attribute the aim of inventory audit to the following factors:
1. Stock record accuracy.
2. Early discovery of inventory problem and immediate resolution.
3. Gross to net calculation accuracy.
4. Effective customer service as a result of on-time order fulfillment
5. Better planning based on accurate stock status
Frequency of Audit
How often inventory counting occurs is termed cycle frequency. As asserted earlier, auditing is quite important to the Financial Controller and the Planning Manager. The Financial Controller can be pretty comfortable with auditing inventory records annually. The planner is most likely to perform inventory audit more often - daily, weekly, monthly or annually.When to AuditIt is good practice to define cycle frequency for an item in the system. The challenge is, when should inventory be counted?
The following can be used as guidelines in facing the challenge.
1. Before an order transaction is created.
2. On receipt of an order.
3. When inventory level is zero.
4. After a defined number of transactions have been carried out.
5. When an emergency count is needed.e.g questionable negative stock.
The Process in SAP Business One
The inventory counting system in SAP Business One is feature rich enough to meet the auditing needs of small and medium scale businesses. With SAP Business One, controls can be set up to eliminate errors that might arise as a result of inventory posting activities during physical counting. This can be achieved by activating the locking feature of an item or warehouse in the item master data - check the Locked indicator. Alternatively, you can disable the document numbering functionality - Administration > System Initialization > Document Numbering - check the Locked field.SAP Business One adheres strictly to due process of inventory counting (see 2nd paragraph - The Concept). This transaction can be achieved by accessing the following path. Inventory > Inventory Transaction > Beginning Quantities, Inventory Tracking Stock Posting.
SAP Business One and Inventory Differences
In most cases, after inventory count, discrepancies often occur between the supposed stock value and the actual stock value, hence the need to reconcile the inconsistencies. As a matter of fact, SAP Business One requires you to post the variance in order to modify the stock value in accounting. This functionality is achieved by accessing this path: Inventory > Inventory Transactions > Beginning Quantities, Inventory Tracking Stock Posting. Select the stock posting Tab. The screen displayed is shown below.
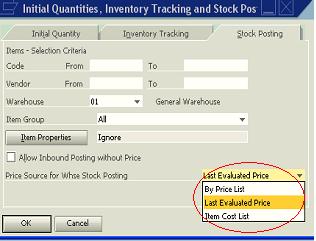
For increased flexibility, SAP Business One provides three options in which the value of an item can be calculated, namely: Price List, Last Revaluation Price and Cost Price. What is more? Only the quantity of an item will be modified when Allow Inbound Posting without Price field is activated. It is important to note that, when the cost price list is chosen in the Price Source for Whse Stock Posting field, the current cost must be recalculated before the variances are posted in the system using the inventory valuation report.
SAP Business One and Cycle Frequency
SAP Business One allows you to define the frequency, alert date and time for your inventory count. This can be achieved by accessing this path: Administration > Setup > Inventory > Inventory Cycles.The following frequency can be defined: Daily, Weekly, Every 4 weeks, Monthly, Quarterly, Semi-annually, Annually and One-time. Furthermore, a comprehensive report recommendation for all scheduled inventory count can be generated in SAP Business One. The alert integration serves as a reminder functionality based on predefined time.
Recommendations
By and large, we have critically analyzed the concept and features of cycle counting and how SAP Business One can be leveraged in this direction. Irrespective of the effectiveness of an inventory counting system, whether in-built in an ERP system or standalone, the human factor is key to the accuracy of inventory records. The following points are recommended steps to be taken, especially as it relates to the human factor.
1. Comprehensive numbering and item description system. This will go a long way to drive correct and easy identification of items
2. Quantity Verification and Price: Considerable time should be spent in posting transaction fields, especially the quantity and price. Basically, the stock quantity affects the stock level and stock value at any point in time
3. On-time transaction entry and execution: It's not enough to just record transactions into the system. Transactions should be recorded as at when due and the physical movement of the goods must be carried out accordingly.
4. Use trained expert: Personnel concerned with stock taking and counting must be highly skilled in the field. It's not a job for dummies!
5. Warehouse safety and security: Wharehouses must be locked and protected at defined time, especially when transactions are not taking place, say at night. This is to prevent stock damage, inventory pilfering and theft.
Cycle Counting is a necessary action in inventory management. The implication of wrong inventory can be grave for a company. It not only mislead in the available stock quantity, but also in the actual stock value - accounting. A number of practices can be leveraged when auditing inventory, however, in this paper, I intend to explore cycle counting as an inventory audit tool. This subject topic will be discussed in the following parts: The Concept, Why Inventory Audit, Frequency of Audit, When to Audit, The Process in SAP Business One and Recommendations.
The Concept
A few months ago, my colleague and I went for a management demo of SAP Business One for a leading bookshop in Nigeria. And you know what? The Chief Financial Officer asked a fundamental question: What happens if I've got some stocks physically in my warehouse and the system displays zero stock, will I be able to sell? What's on your mind, negative stock management? Well, that concept is a topic for another posting. Well, for me, what struck me was inventory record inaccuracy. The nightmare of an entrepreneur among other things includes the correctness of his stock record, hence the need for a stock auditing infrastructure like Cycle Counting. This kind of system is provided in SAP Business One.
Thus, it is expedient that inventory be counted at defined intervals and if variances occur, it should be reconciled. The process of inventory audit follows some sequential steps as detailed below.
1. Print out the inventory status from the system
2. Perform the physical count of the item and record your findings
3. Ascertain the correctness of the count by recounting
4. Record the count result in the system
5. If variances occur, post the stock difference.
As a matter of fact, inventory records are not always 100% accurate. Variances do occur, depending on the item type, volatility and frequency of movement. Hence, tolerance (in %) can be defined to cover this lapse. However, as much as possible, 100% accuracy should be the target.Why Inventory Audit The need for inventory audit is enormous. Broadly, inventory audit is of great interest and importance to two sets of people in a firm - the Financial Controller and the Planning Manager. While the Financial Controller is concerned about the accuracy of the stock value, the Planning Manager is concerned about the accuracy of the stock quantity. In whichever way you look at it, the stock quantity is the driver of the stock value. For the Financial Controller to know the correct stock value, the stock quantity must have been duly counted and multiplied by the cost of the item.
From the foregoing therefore, we can safely attribute the aim of inventory audit to the following factors:
1. Stock record accuracy.
2. Early discovery of inventory problem and immediate resolution.
3. Gross to net calculation accuracy.
4. Effective customer service as a result of on-time order fulfillment
5. Better planning based on accurate stock status
Frequency of Audit
How often inventory counting occurs is termed cycle frequency. As asserted earlier, auditing is quite important to the Financial Controller and the Planning Manager. The Financial Controller can be pretty comfortable with auditing inventory records annually. The planner is most likely to perform inventory audit more often - daily, weekly, monthly or annually.When to AuditIt is good practice to define cycle frequency for an item in the system. The challenge is, when should inventory be counted?
The following can be used as guidelines in facing the challenge.
1. Before an order transaction is created.
2. On receipt of an order.
3. When inventory level is zero.
4. After a defined number of transactions have been carried out.
5. When an emergency count is needed.e.g questionable negative stock.
The Process in SAP Business One
The inventory counting system in SAP Business One is feature rich enough to meet the auditing needs of small and medium scale businesses. With SAP Business One, controls can be set up to eliminate errors that might arise as a result of inventory posting activities during physical counting. This can be achieved by activating the locking feature of an item or warehouse in the item master data - check the Locked indicator. Alternatively, you can disable the document numbering functionality - Administration > System Initialization > Document Numbering - check the Locked field.SAP Business One adheres strictly to due process of inventory counting (see 2nd paragraph - The Concept). This transaction can be achieved by accessing the following path. Inventory > Inventory Transaction > Beginning Quantities, Inventory Tracking Stock Posting.
SAP Business One and Inventory Differences
In most cases, after inventory count, discrepancies often occur between the supposed stock value and the actual stock value, hence the need to reconcile the inconsistencies. As a matter of fact, SAP Business One requires you to post the variance in order to modify the stock value in accounting. This functionality is achieved by accessing this path: Inventory > Inventory Transactions > Beginning Quantities, Inventory Tracking Stock Posting. Select the stock posting Tab. The screen displayed is shown below.
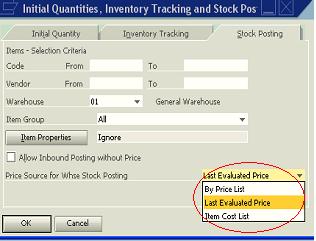
For increased flexibility, SAP Business One provides three options in which the value of an item can be calculated, namely: Price List, Last Revaluation Price and Cost Price. What is more? Only the quantity of an item will be modified when Allow Inbound Posting without Price field is activated. It is important to note that, when the cost price list is chosen in the Price Source for Whse Stock Posting field, the current cost must be recalculated before the variances are posted in the system using the inventory valuation report.
SAP Business One and Cycle Frequency
SAP Business One allows you to define the frequency, alert date and time for your inventory count. This can be achieved by accessing this path: Administration > Setup > Inventory > Inventory Cycles.The following frequency can be defined: Daily, Weekly, Every 4 weeks, Monthly, Quarterly, Semi-annually, Annually and One-time. Furthermore, a comprehensive report recommendation for all scheduled inventory count can be generated in SAP Business One. The alert integration serves as a reminder functionality based on predefined time.
Recommendations
By and large, we have critically analyzed the concept and features of cycle counting and how SAP Business One can be leveraged in this direction. Irrespective of the effectiveness of an inventory counting system, whether in-built in an ERP system or standalone, the human factor is key to the accuracy of inventory records. The following points are recommended steps to be taken, especially as it relates to the human factor.
1. Comprehensive numbering and item description system. This will go a long way to drive correct and easy identification of items
2. Quantity Verification and Price: Considerable time should be spent in posting transaction fields, especially the quantity and price. Basically, the stock quantity affects the stock level and stock value at any point in time
3. On-time transaction entry and execution: It's not enough to just record transactions into the system. Transactions should be recorded as at when due and the physical movement of the goods must be carried out accordingly.
4. Use trained expert: Personnel concerned with stock taking and counting must be highly skilled in the field. It's not a job for dummies!
5. Warehouse safety and security: Wharehouses must be locked and protected at defined time, especially when transactions are not taking place, say at night. This is to prevent stock damage, inventory pilfering and theft.
1 Comments:
At 4:51 PM, June 13, 2006,
Kehinde Disu said…
Hi All the best!
Sounds great!
Thanks
Post a Comment
<< Home